Gubras
The Guardian for Rotating Equipment
Industries We Serve

Data Acquisition card: Flexibility in installation of new sensors and gathering data from preinstalled systems.

Fault Detection card: State-of-the-art fault detection methods utilizing our expert knowledge in design and maintenance of rotary equipment.

Decision Support card: Gaining insights through applications of AI and plantwide integrated databases. Connections to other management tools and software.

Cyber Security card: Security Checklist policy base on ISA/IEC 62443 ISO/IEC 27001
Gubras
The guardian for rotating equipment
Gubras Matrix
Gubras Kernel
Gubras Kernel is a powerful gateway in charge of receiving data from the DAQ systems and the DCS, aggregating and storing the data, calculating performance parameters, and performing fault detection and fault isolation algorithms, as well as sending the reports, data, alerts, and results to our user interface.
Gubras Kernel
Gubras Visage is our main user interface. It utilizes different real-time 2d and 3d charts and models, as well as multiple trend analysis methods and function to provide all the tools required for predictive maintenance and condition monitoring of rotating equipment.
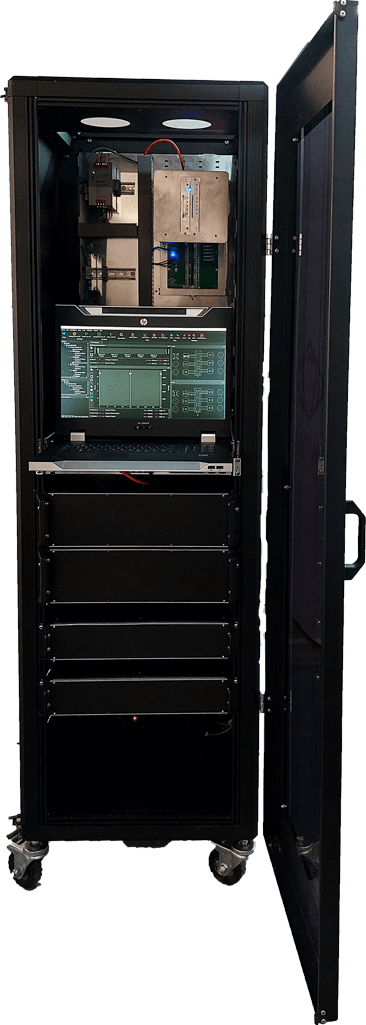
Beyond Protection
Comprehensive monitoring
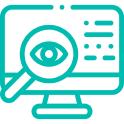
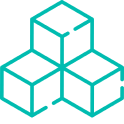
Component model
Reciprocating compressors solution
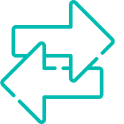

Scalability
Full customer support
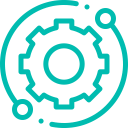
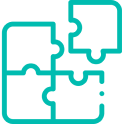
Portable solution

Step 1
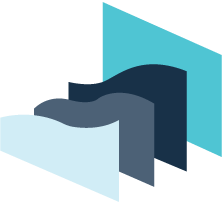
Step 2
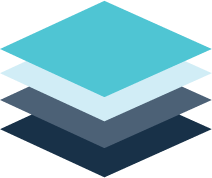